Common Pain Points in the Distribution of Chemicals Customers come to us disillusioned from their experiences with other carriers in the distribution of chemicals, suffering from similar logistics issues. Once you’ve been in the chemical distribution game for as long as we have (four decades and counting!), you start to notice certain themes.
When it comes to the distribution of chemicals, there are some common pain points most people encounter before they find us. As it turns out, these pain points are interrelated.
But even more importantly, they can be avoidable in most cases.
At All Chemical, we know these pain points well—and we’ve designed our operation to rescue you from them!
Logistics Issue #1: Multi-Vendor Syndrome
This pain point is so common we gave it a name: “multi-vendor syndrome.” We see it constantly, with customers contracting with one carrier for transit, and yet another for storage, washing, and servicing. Suddenly there are multiple points of contact, invoices coming from all directions—even product transfers gone wrong that were unnecessary in the first place. The more links in the chain, the more places the chain can break.
Instead, at All Chemical, we handle every aspect of a haul from start to finish. As specialists in the distribution of chemicals, we provide every service our customers need in-house. No more juggling several vendor relationships with their separate fluid logistics issues! We give our customers the full-service treatment, offering a wide array of services from tank washing and steaming, to storage, loading, transloading, equipment servicing, and delivery.
Logistics Issue #2: Equipment Limitations
Then there’s the problem of carriers’ limited equipment offerings. We hear regularly from customers who contracted with a chemical distributor, only to find out after they’d taken load possession that the carrier’s operation doesn’t have the precise equipment needed for a later stage of the haul. Sure, sometimes the carrier can refer out, contract with a second or third vendor to fill in the gaps. But the problem with this? You guessed it—it leads directly to multi-vendor syndrome.
We at All Chemical prefer to head off this issue at the pass. Our growing intermodal fleet and cutting-edge equipment can handle an astonishing load capacity array, safely hauling chemicals of most varieties such as hazardous, non-hazardous, food-grade, Kosher, organic, and inorganic.
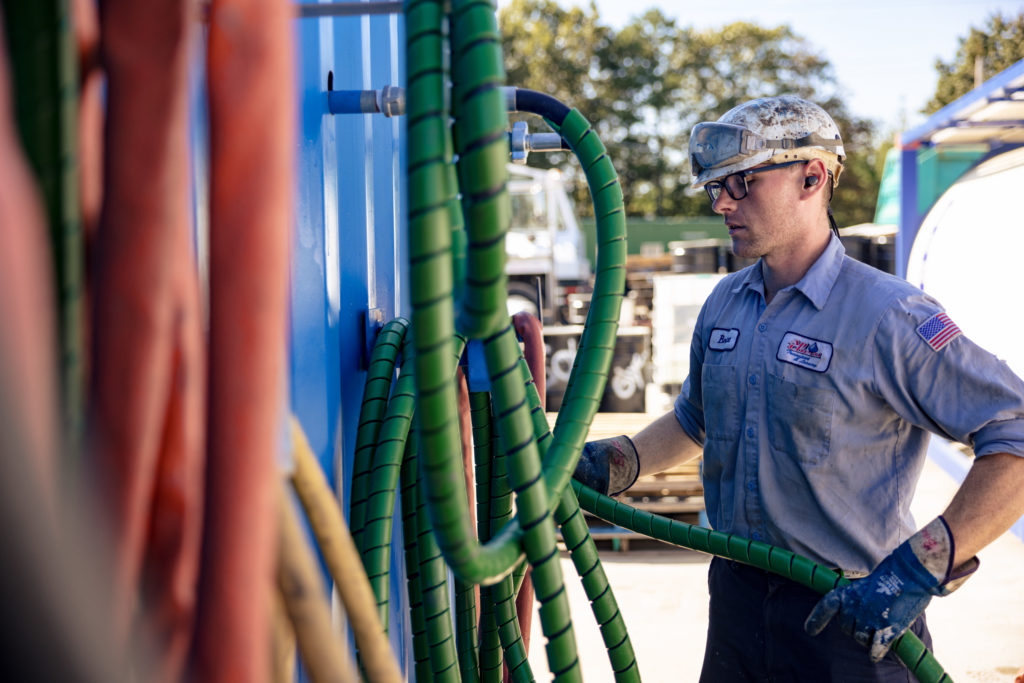
Logistics Issue #3: The “Size Paradox”
A final common pain point plaguing customers is the “Size Paradox.” Customers trying to avoid frustrating customer service experiences associated with big carriers often opt for a small, hands-on, Mom-and-Pop-style carrier, hoping that they’ll get quality attention and prompt service.
But then they find themselves victim to issues of equipment limitation, as the small carrier can’t cover all the bases the job needs. (This discovery always seems to happen right in the middle of a job!) Suddenly, the customer is trapped in multi-vendor syndrome, frantically juggling several vendors just to complete a single haul.
They come away swearing never to go through such a headache again. So, for their next haul, they opt for a big-name, big-operation chemical distributor, hoping equipment limitation won’t be a problem and multi-vendor syndrome won’t ever come up.
And that’s when they discover just how awful it is to be nothing more than a number on another invoice, waiting interminably on hold, not even sure who to talk to about any logistics issues that arise.
We hear story after story from customers who land in messes like these. Through tireless effort and commitment, we keep our business in the sweet spot: where our dedicated team is small enough to know every customer we serve, yet our operation is large enough to cover all the bases you could possibly need.
So, if you’ve suffered from these common pain points in the distribution of chemicals, give us a call. Discover for yourself how we at All Chemical can put those pain points in your rearview mirror—for good!